Ball mills rotate around a horizontal axis, partially filled with the material to be ground plus the grinding medium.
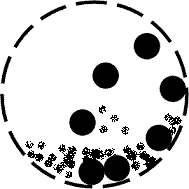
Different materials are used as media, including ceramic balls, flint pebbles and stainless steel balls. An internal cascading effect reduces the material to a fine powder.
Industrial ball mills can operate continuously, fed at one end and discharged at the other end. Large to medium-sized ball mills are mechanically rotated on their axis, but small ones normally consist of a cylindrical capped container that sits on two drive shafts (pulleys and belts are used to transmit rotary motion).
A rock tumbler functions on the same principle. Ball mills are also used in pyrotechnics and the manufacture of black powder, but cannot be used in the preparation of some pyrotechnic mixtures such as flash powder because of their sensitivity to impact. High-quality ball mills are potentially expensive and can grind mixture particles to as small as 5 nm, enormously increasing surface area and reaction rates. The grinding works on the principle of critical speed. The critical speed can be understood as that speed after which the steel balls (which are responsible for the grinding of particles) start rotating along the direction of the cylindrical device; thus causing no further grinding.
Ball mills are used extensively in the mechanical alloying process[1] in which they are not only used for grinding but for cold welding as well, with the purpose of producing alloys from powders.[2]
Lead antimony grinding media with aluminium powder.
A ball mill inside the Mayflower Mill near Silverton, Colorado.
The ball mill is a key piece of equipment for grinding crushed materials, and it is widely used in production lines for powders such as cement, silicates, refractory material, fertilizer, glass ceramics, etc. as well as for ore dressing of both ferrous non-ferrous metals. The ball mill can grind various ores and other materials either wet or dry. There are two kinds of ball mill, grate type and overfall type due to different ways of discharging material. There are many types of grinding media suitable for use in a ball mill, each material having its own specific properties and advantages. Key properties of grinding media are size, density, hardness, and composition.
Size: The smaller the media particles, the smaller the particle size of the final product. At the same time, the grinding media particles should be substantially larger than the largest pieces of material to be ground.
Density: The media should be denser than the material being ground. It becomes a problem if the grinding media floats on top of the material to be ground.
Hardness: The grinding media needs to be durable enough to grind the material, but where possible should not be so tough that it also wears down the tumbler at a fast pace.
Composition: Various grinding applications have special requirements. Some of these requirements are based on the fact that some of the grinding media will be in the finished product. Others are based in how the media will react with the material being ground.
Where the color of the finished product is important, the color and material of the grinding media must be considered.
Where low contamination is important, the grinding media may be selected for ease of separation from the finished product (i.e.: steel dust produced from stainless steel media can be magnetically separated from non-ferrous products). An alternative to separation is to use media of the same material as the product being ground.
Flammable products have a tendency to become explosive in powder form. Steel media may spark, becoming an ignition source for these products. Either wet-grinding, or non-sparking media such as ceramic or lead must be selected.
Some media, such as iron, may react with corrosive materials. For this reason, stainless steel, ceramic, and flint grinding media may each be used when corrosive substances are present during grinding.
The grinding chamber can also be filled with an inert shield gas that does not react with the material being ground, to prevent oxidation or explosive reactions that could occur with ambient air inside the mill.
Such a awesome information. We are also a high strength and durable ball mill manufacturers in India.
ReplyDelete